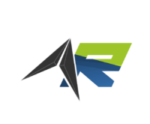
UNAQ RACING
Project
ELECTRATÓN B CATEGORY 2019
Design challenge
Electratón is a project in which students design, build, and compete with an electric car powered by lead-acid batteries or any other technology in a series of 5 races. This initiative promotes the creation of human capital for the Automotive Industry and encourages the development of values such as teamwork, excellence, creativity, innovation, and environmental responsibility.
Each race will have a duration of 1 hour, during which each car must make a pit stop to change batteries, fostering the development of race strategy and teamwork. The car that completes the highest number of laps during this time will be the winner. In the event of a tie in the number of laps, the winner will be determined by the order in which they cross the finish line.
Role
Team Founder
Chasis Design Leader
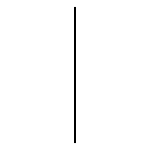
GENERAL RULES AND REQUIREMENTS
Design restrictions
- Car maximum dimensions are 59in x 98in and 45in tall.
- The car must have a front bar of at least 3/4 inch (1.905 cm) in diameter, located at least 2 inches (5.08 cm) away from the pilot’s feet.
- The bars should protect the upper part of the pilot, which must have a minimum height of 8 inches and a maximum height of 14 inches. Likewise, there should be a structural member covering the lower part of the pilot (knees, feet, hips) to prevent any car from entering the pilot’s cabin in the event of an impact.
- Driver must fit inside structure and properly protect him from high speed impacts.
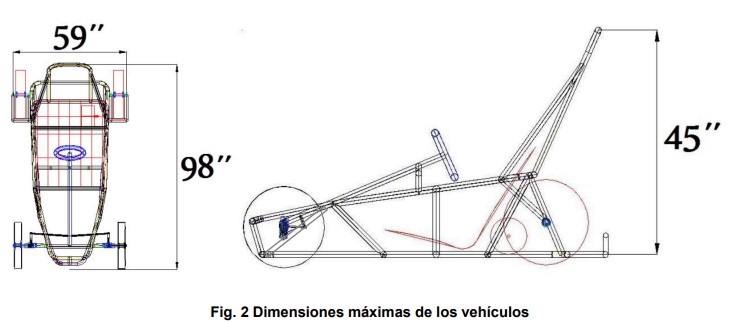
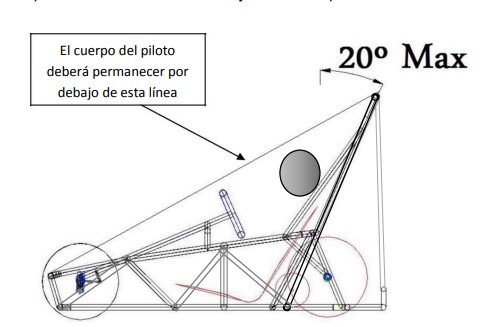
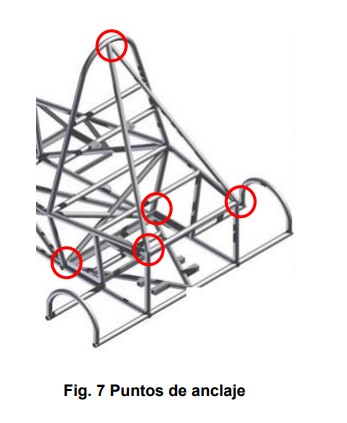
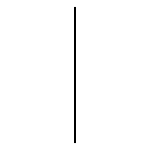
STARTING FROM SCRATCH
As we pioneered in creating this team from scratch we started benchmarking other teams and conducted a wide research on Formula SAE and electric car design in order to start our own first concepts. The first thing I did as team manager is to stablish areas to work in different systems of the car.
Team Areas
-Logistics and sponsorships (PR)
-Chassis design
-Suspension and brakes
-Steering system
-Safety and regulations
-Power train and electronics
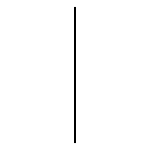
FIRST CONCEPT
Most teams had 4140 steel chassis, we quickly realized that was above our cost range, so we decided to manufacture chassis from 6061 Aluminum.
Using Solidworks we started by creating profile structures using the structural members tool. This tool was very helpful since it allows us to export tubing dimensions directly from Solidworks without the need to design each tubing part individually, saving us valuable time to design more parts.
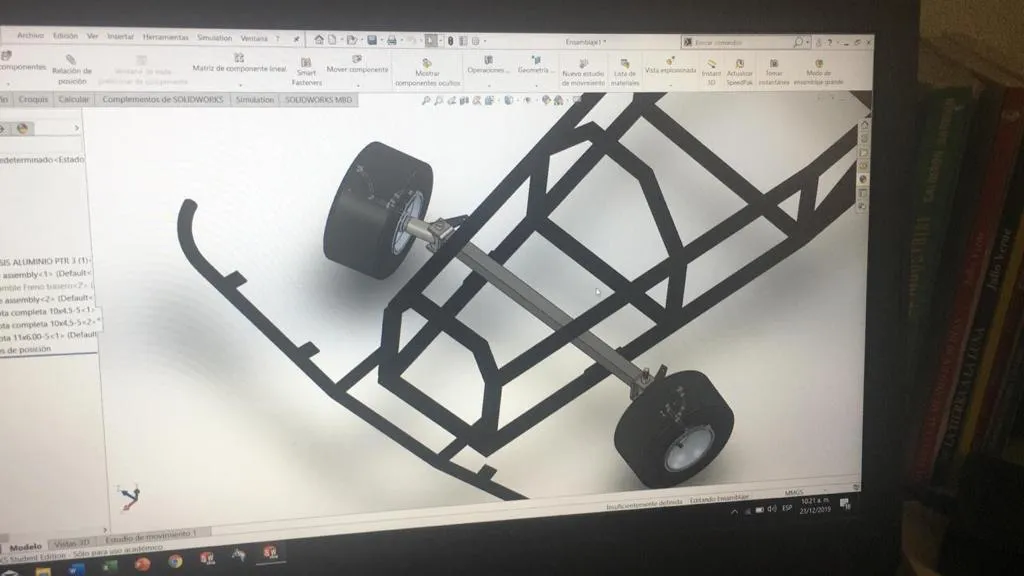
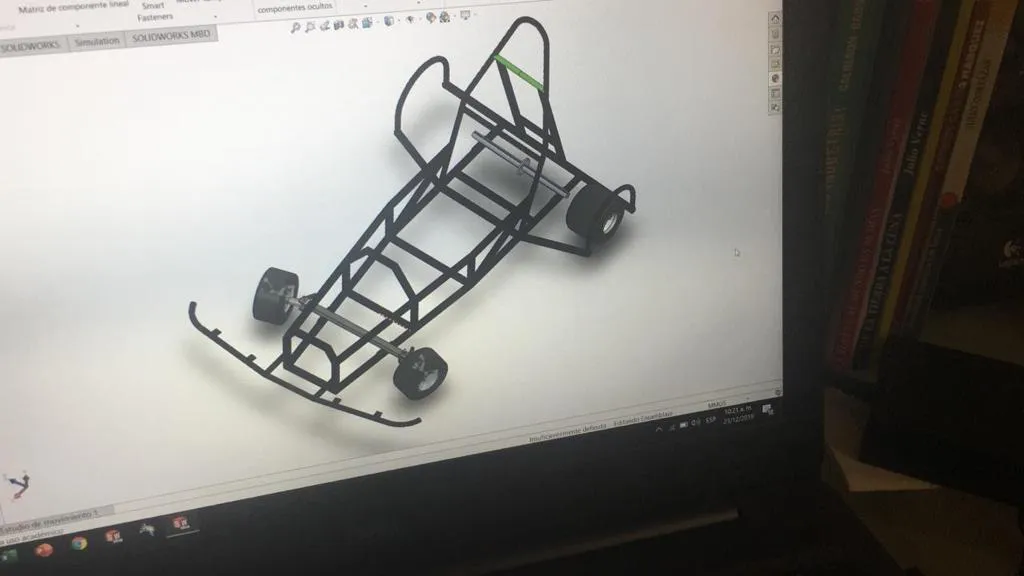
Most teams used rounded profile tubing, but since our most cost-effective solution was to use rectangular shaped tubing since we obtained a sponsorship from a local supplier of aluminum and we also had equipment for soldering aluminum and some experts help.
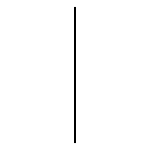
ASSEMBLY DESIGN AND BLUEPRINTS
In order to build the car I designed each blueprint for chassis elements so that specialists in assembly integrate and solder components as specified in the official rules, this are some of the blueprints created, where each structural element had its specifications mentioned.
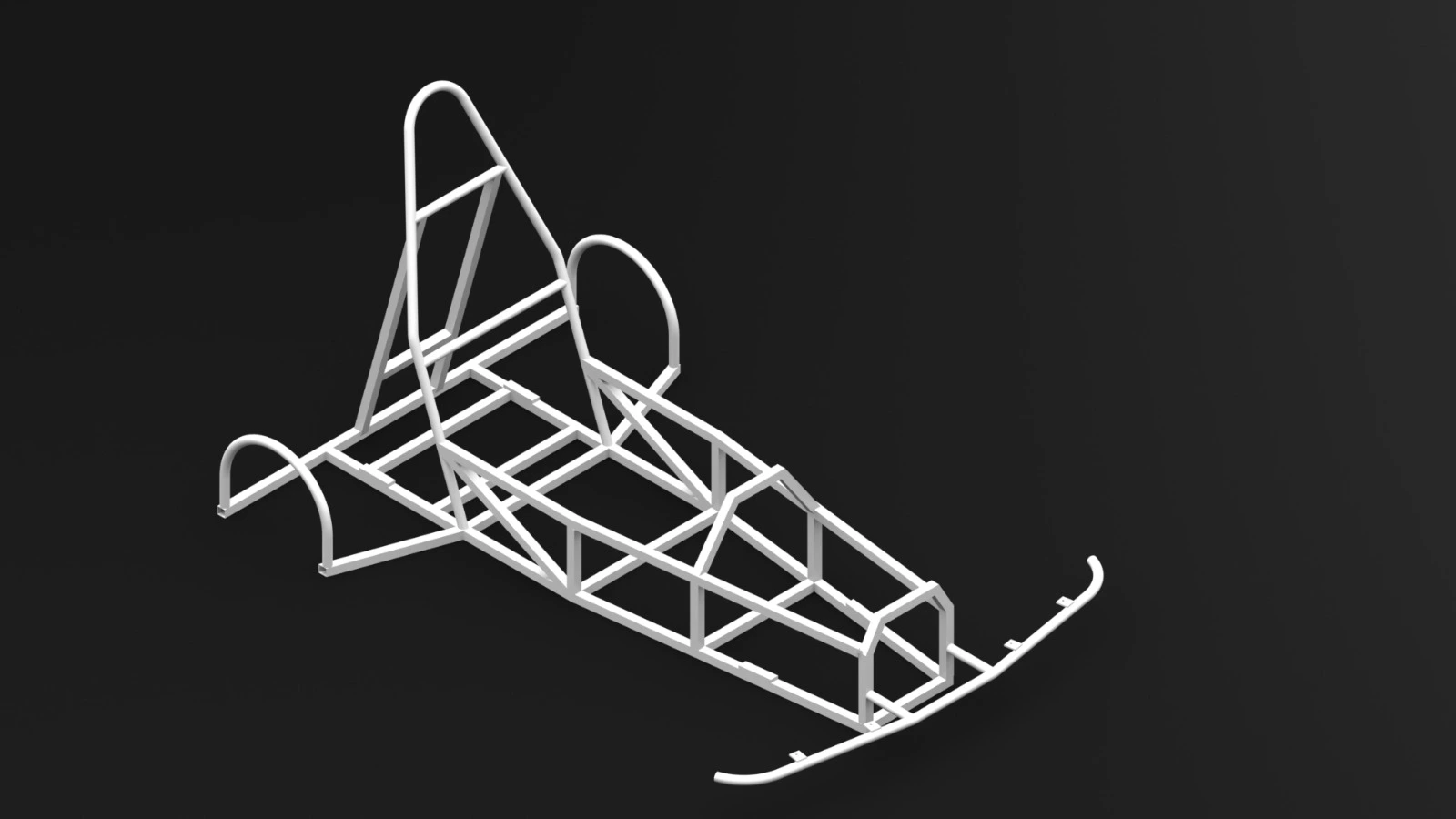
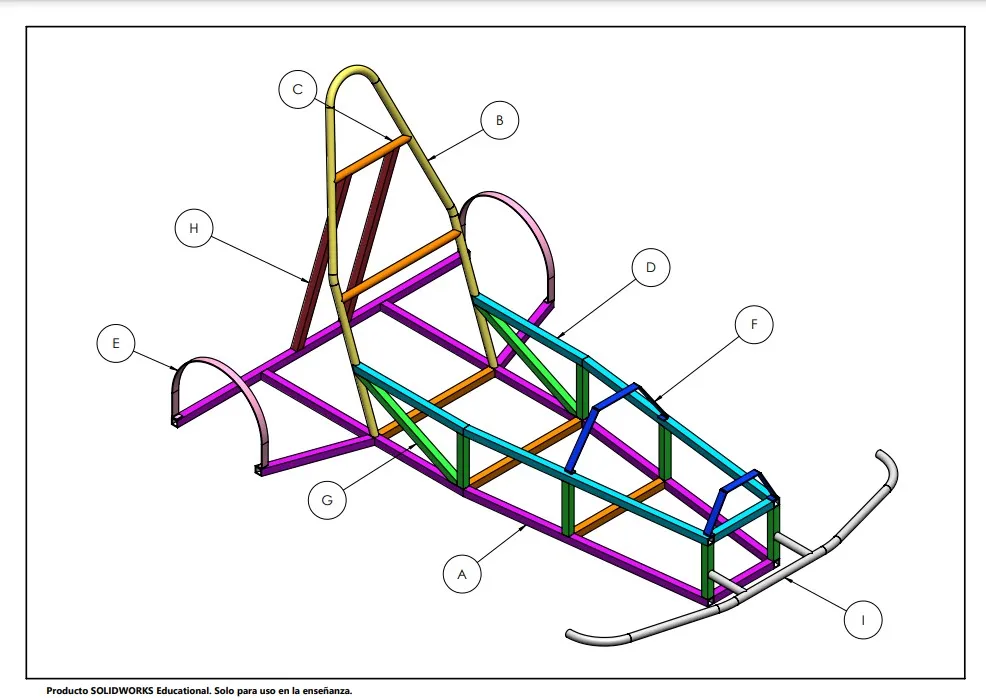
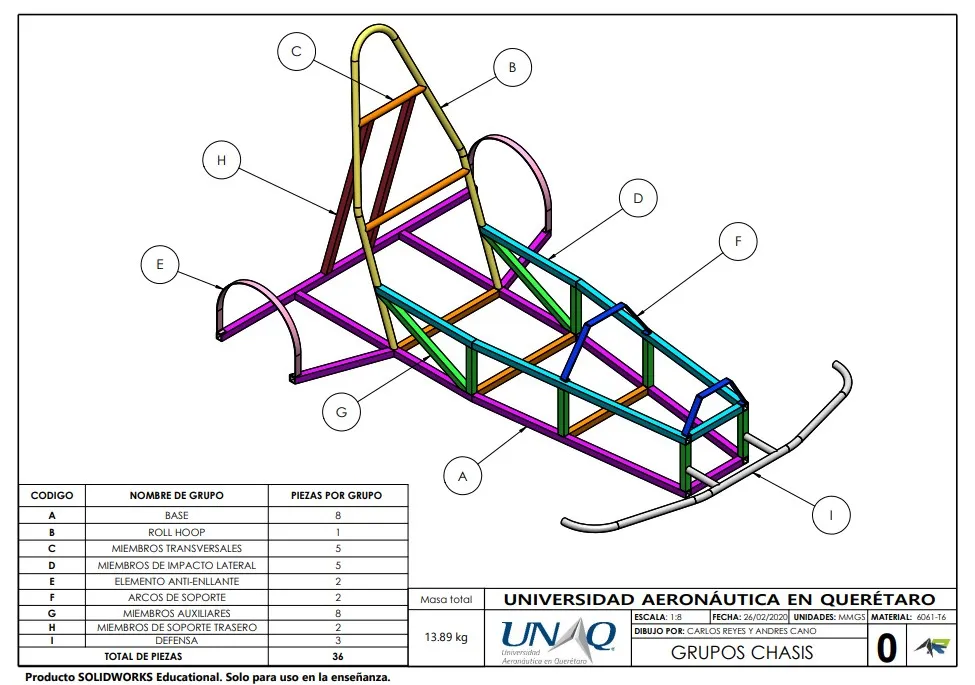
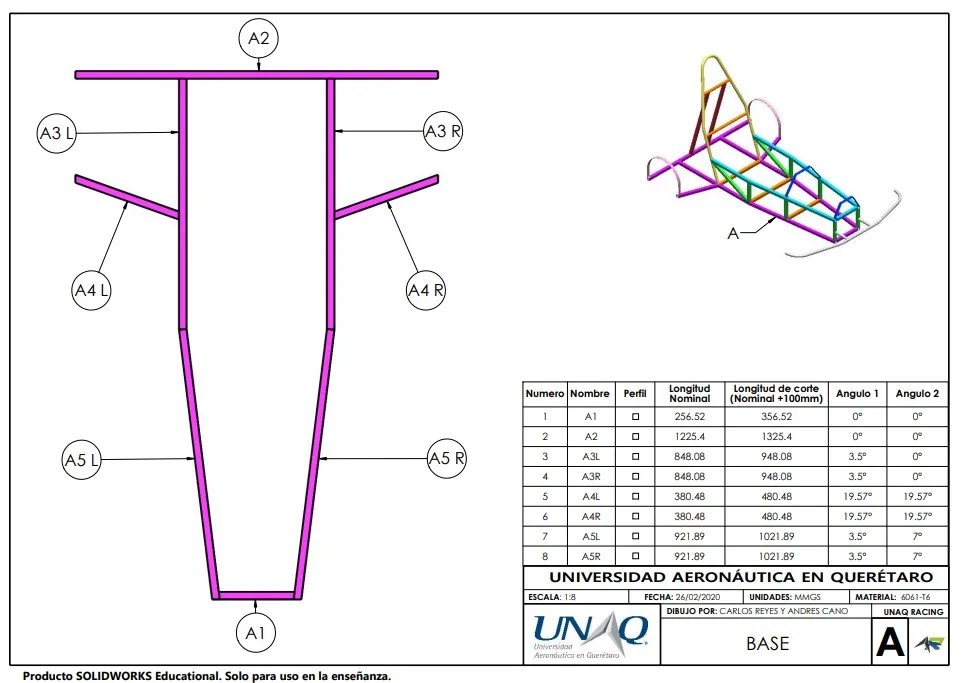
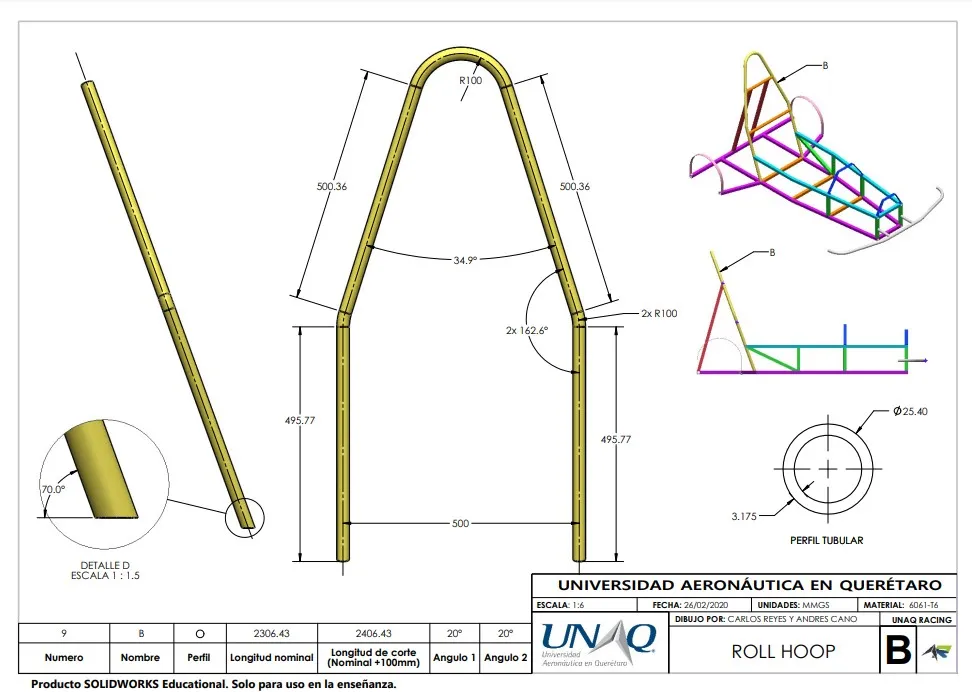
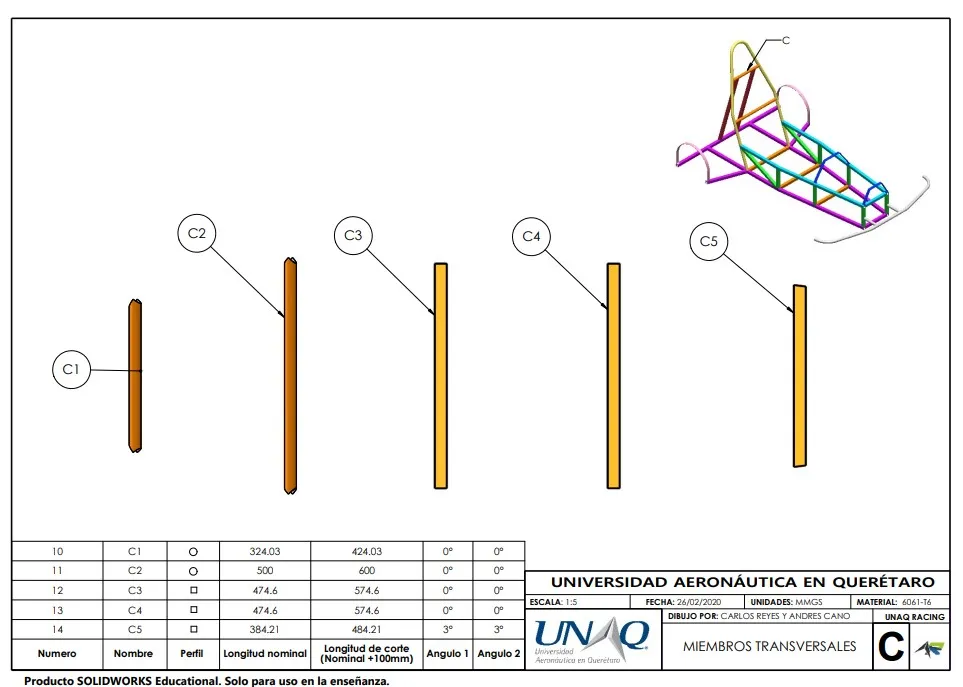
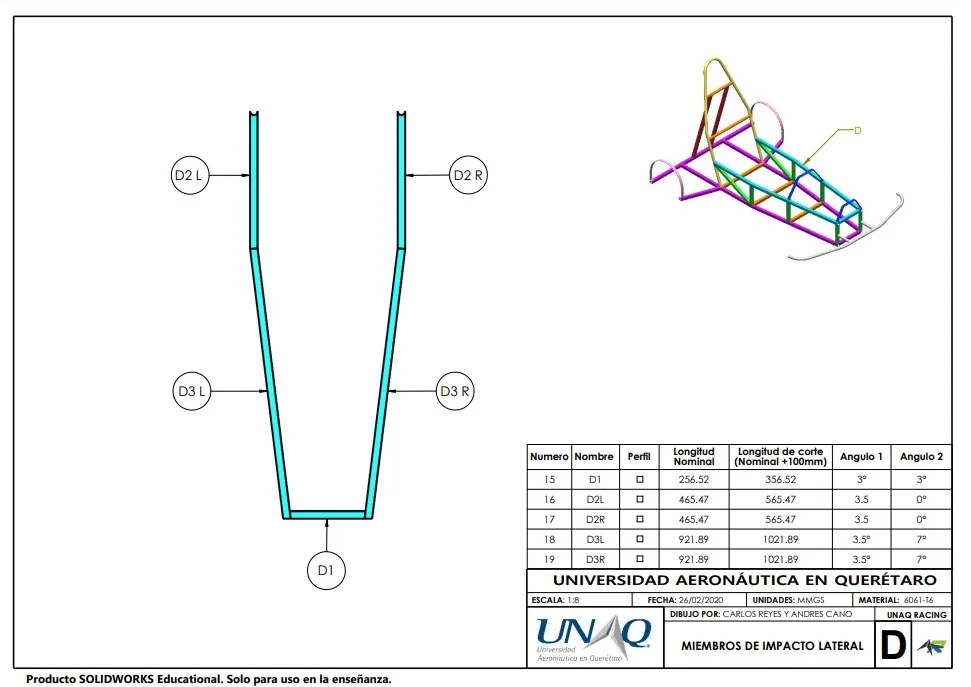
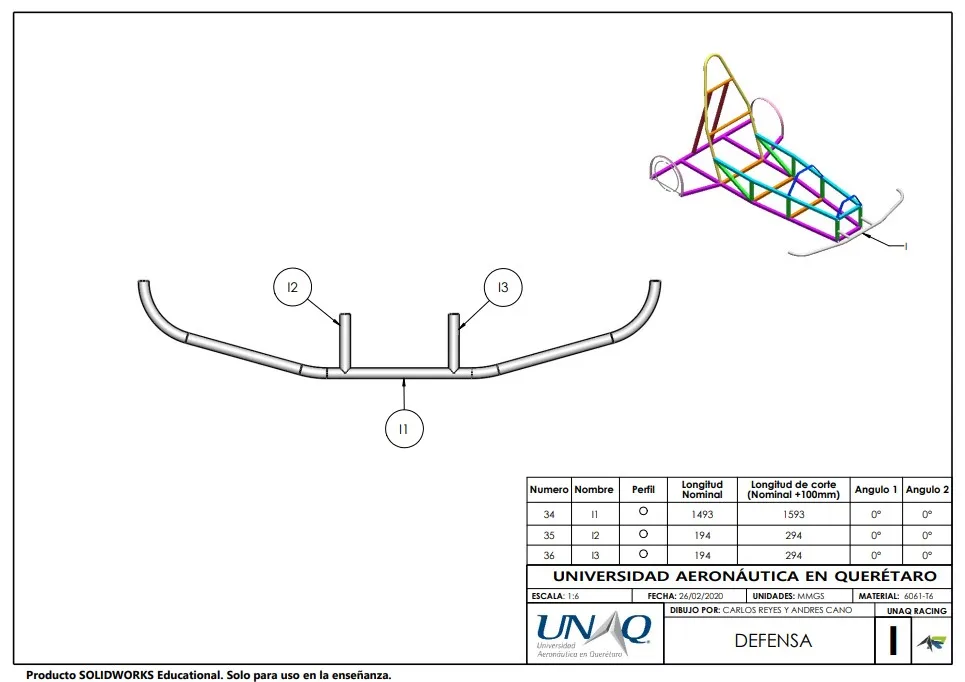
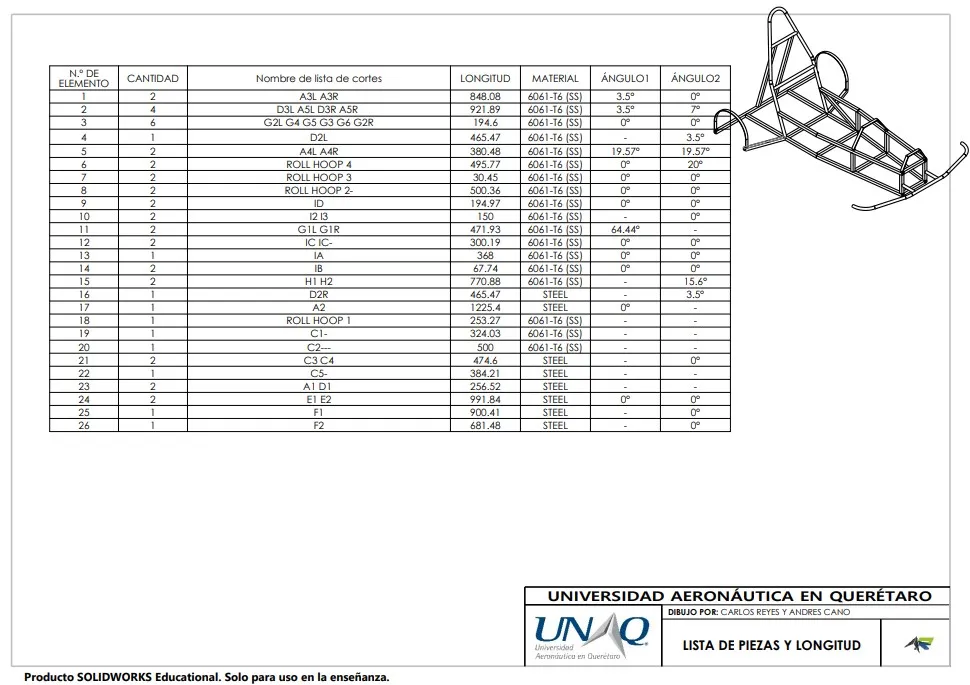
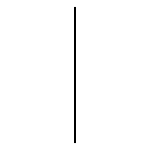
CHASIS FINAL DESIGN
After many iterations and revisions with the team areas we agreed on the final design, and I generated renderings of the chasis design and fiber glass bodyshape of the car
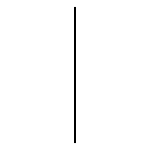
PROTOYPE CONSTRUCTION
Before we actually build the final car we decided to go ahead and make a PVC tubing prototype in order to get a sense of the dimensions of the car and also perform tests with other components and an actual driver.
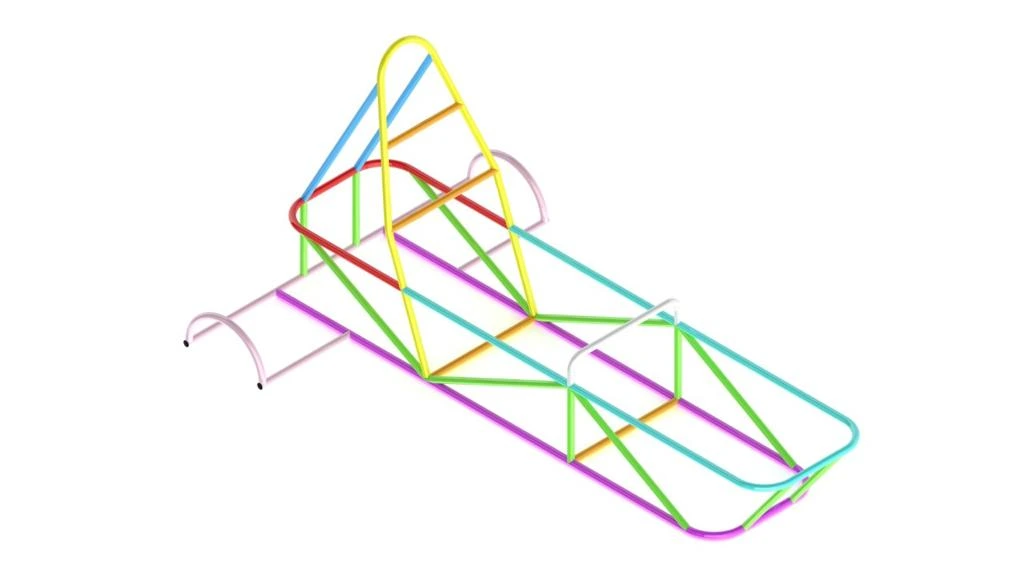
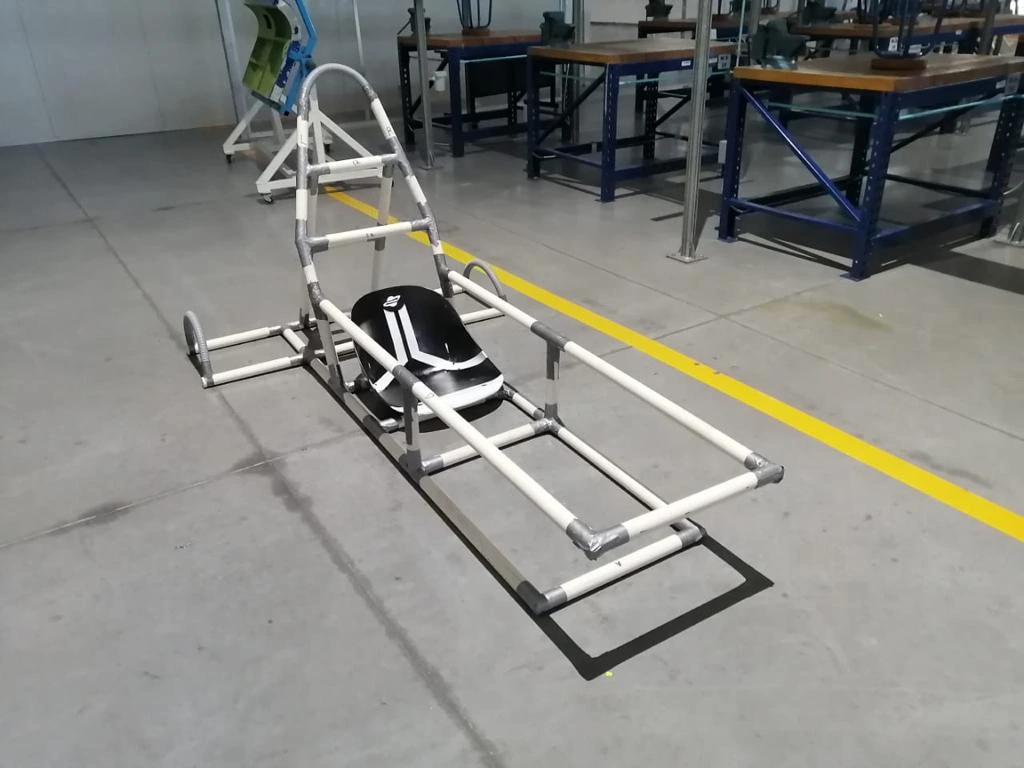
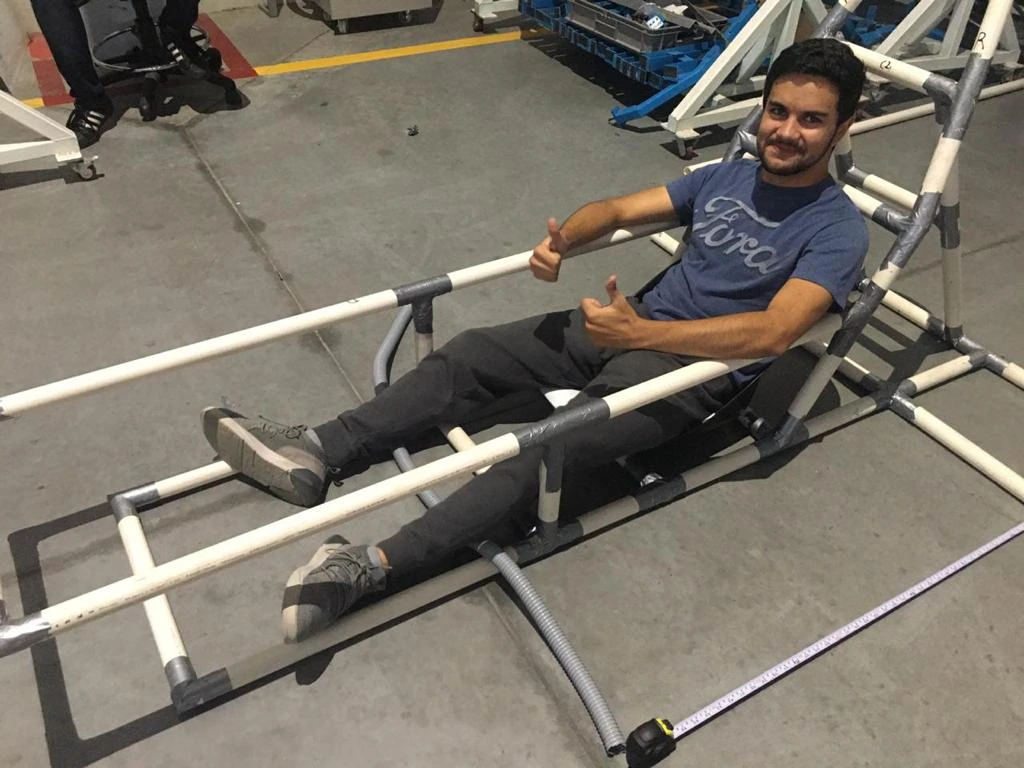
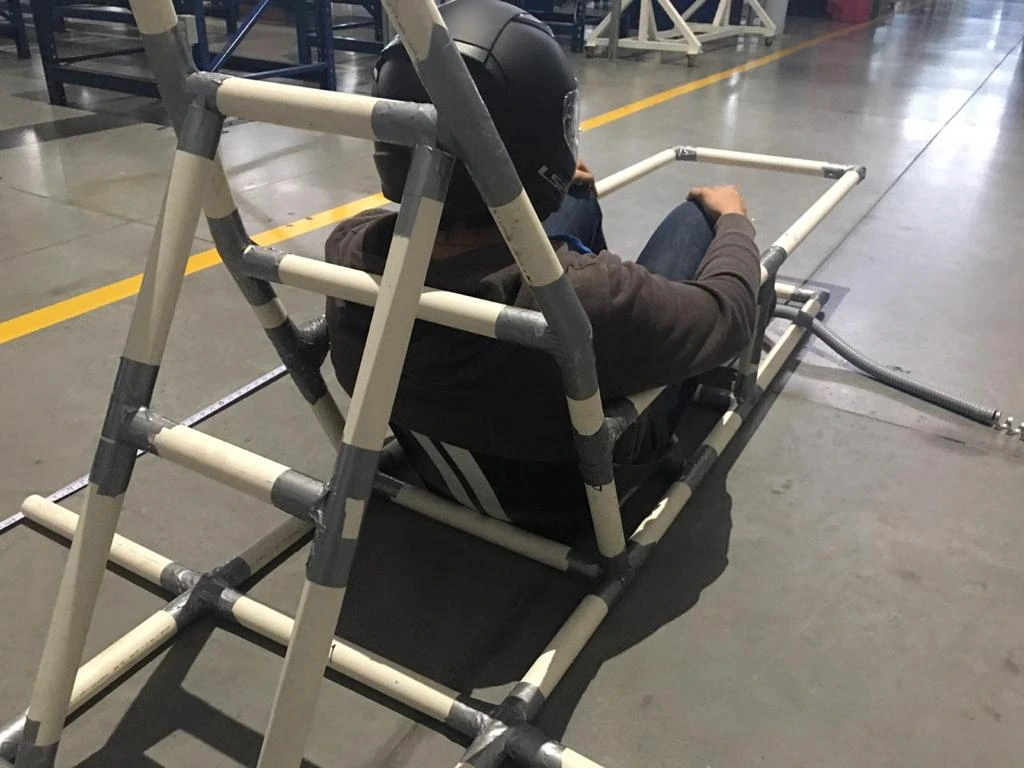
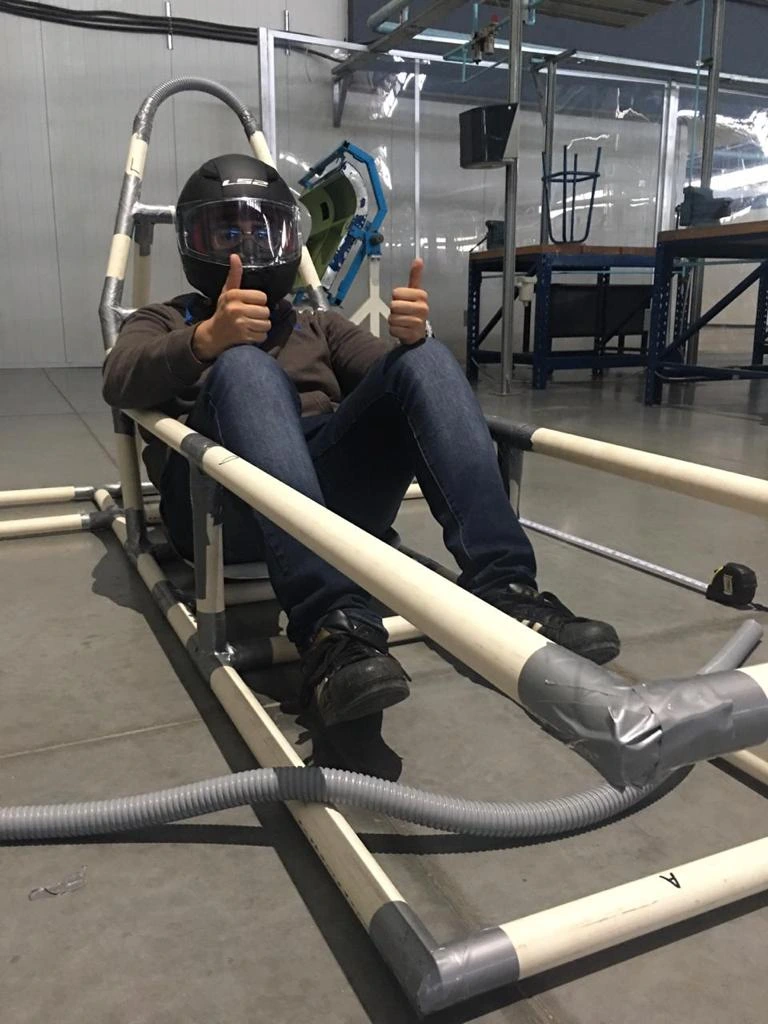
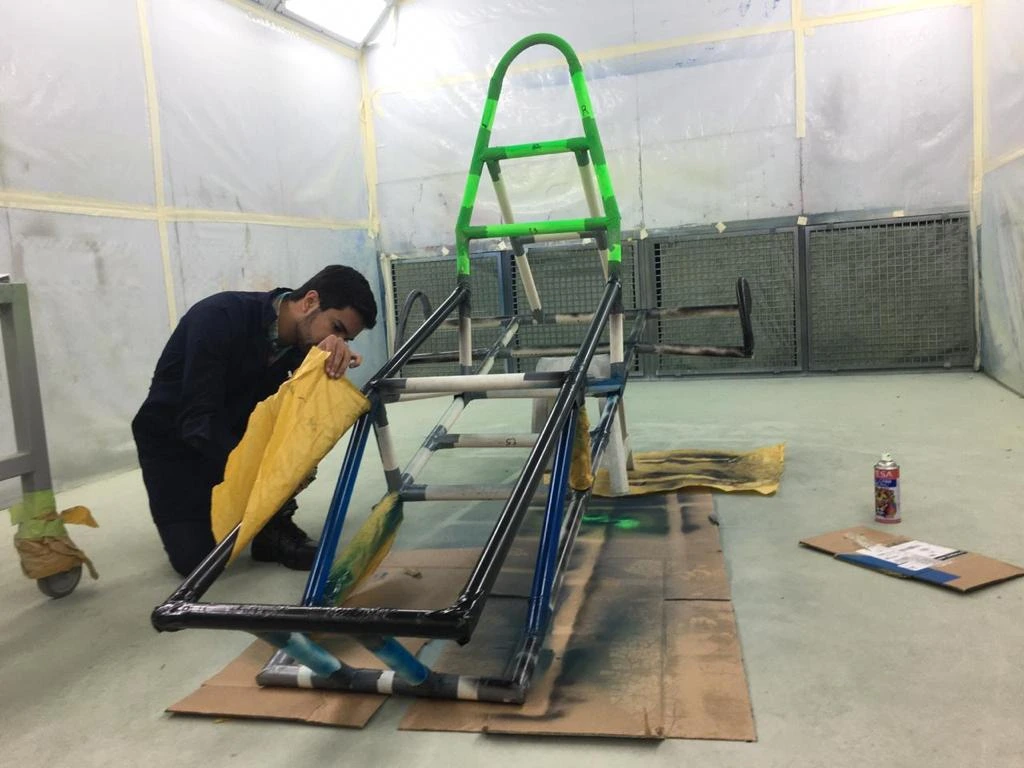
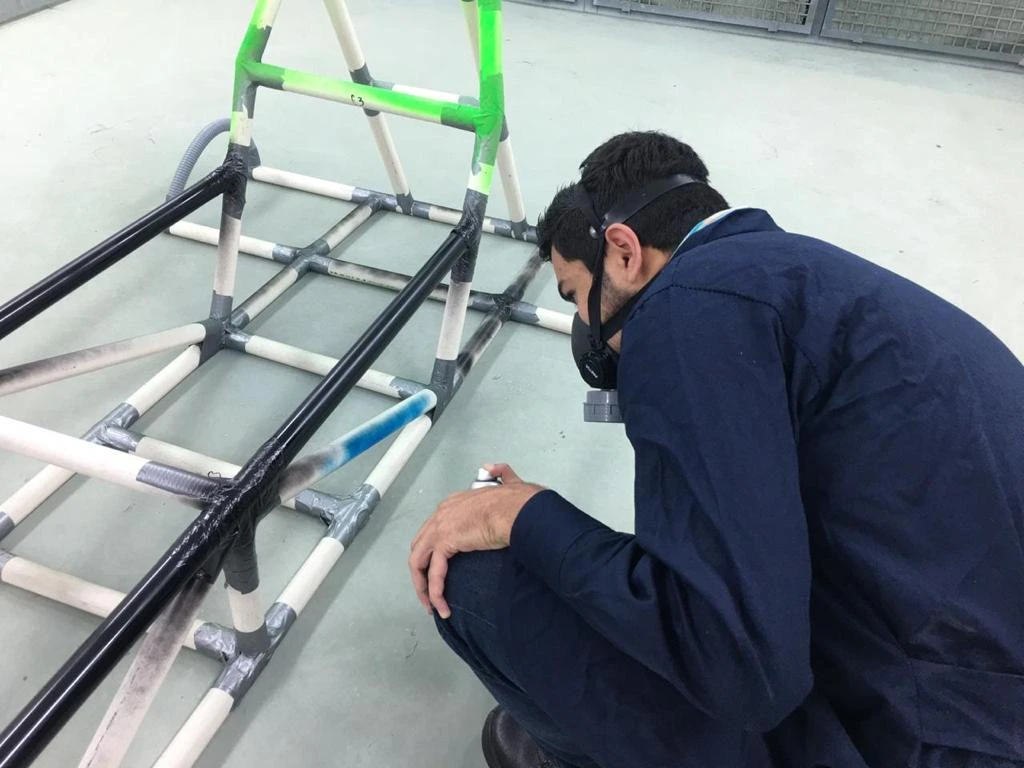
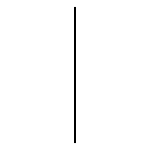
CONSTRUCTION OF CHASSIS
With all blueprints ready and materials we stared construction of the actual chasis
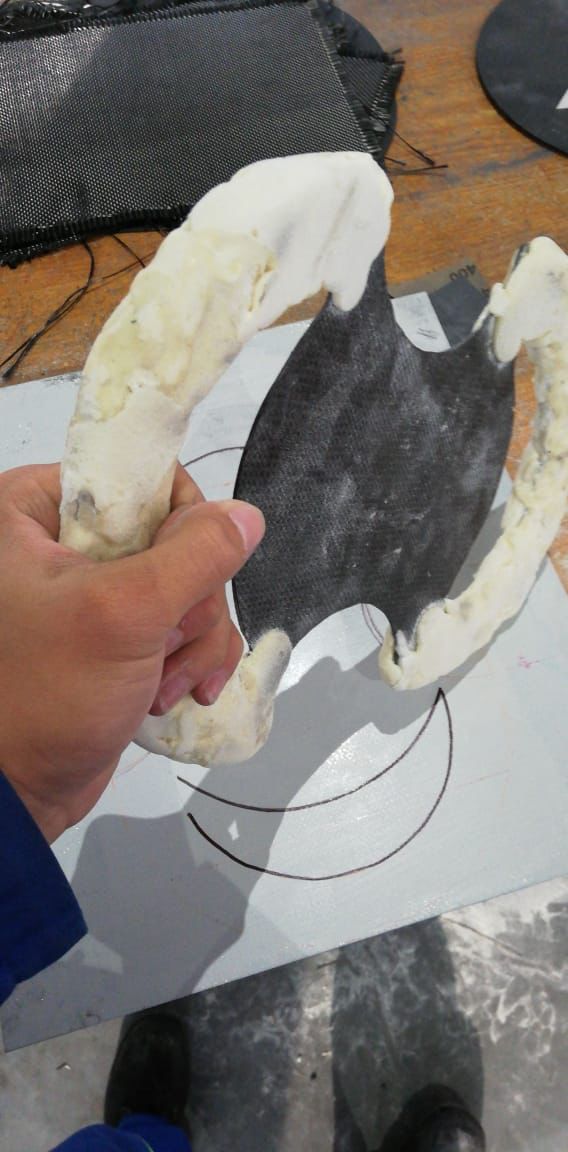
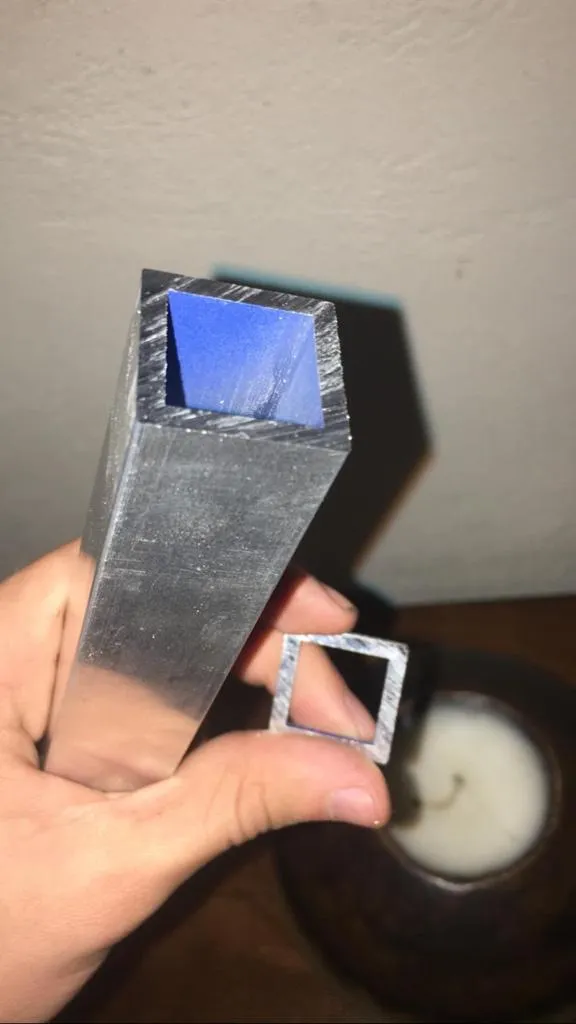
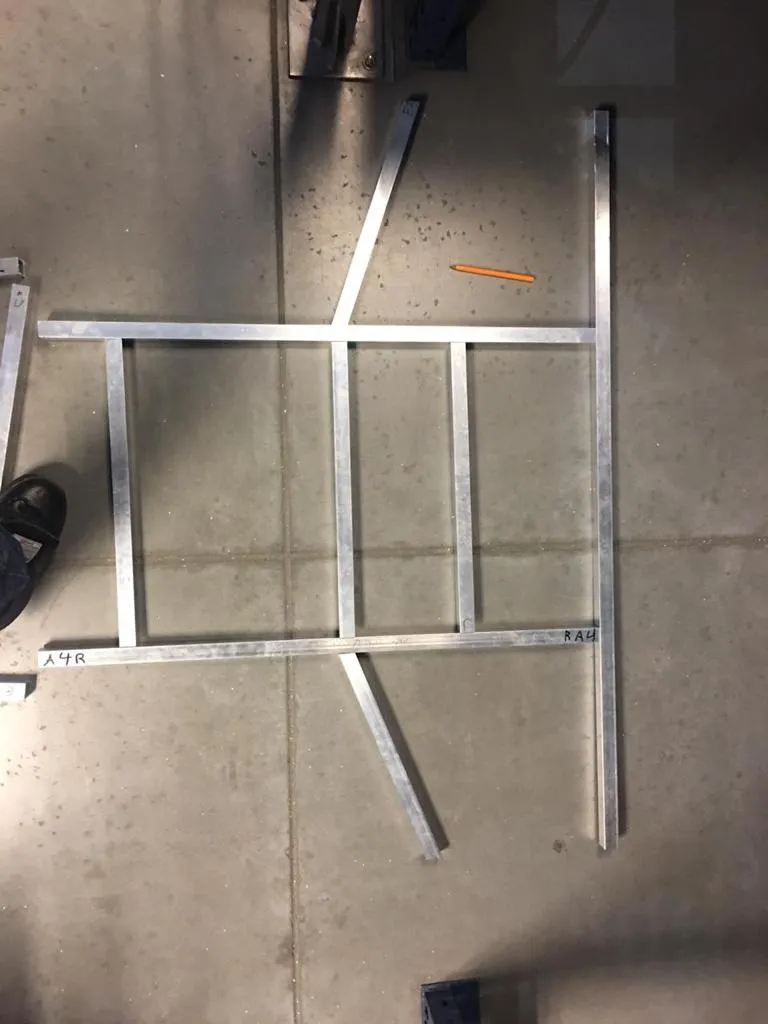
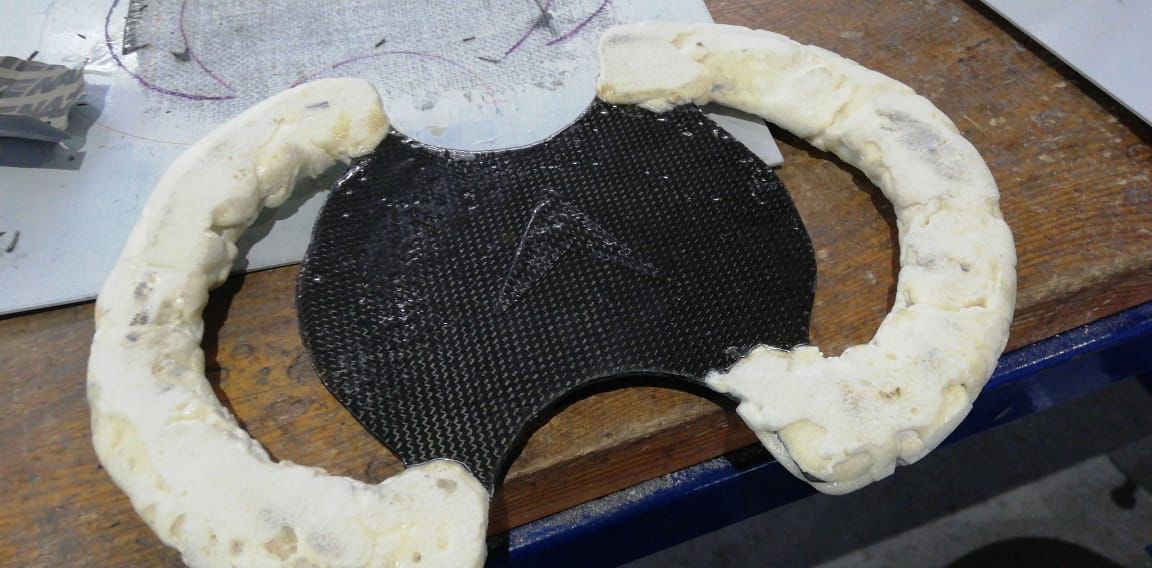
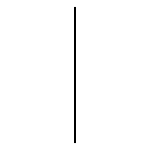
RESULTS AND ACHIEVEMENTS
We successfully constructed the base of the chassis, acquired safety components including professional helmets and gear, and manufactured the steering wheel using carbon fiber.
However, in 2020, the pandemic struck, leading to a complete shutdown of all operations. Our university closed workshop access, and even our providers had to withdraw their support, preventing us from completing the chassis fabrication.
The competition was postponed by the organizers until 2022 due to the pandemic. Unfortunately, during the long period without working on the team, the project was eventually canceled.
Despite this unfortunate situation all of the team members acquired a wide range of abilities and competences, some of the most important are:
Hard skills:
-CAD Modeling
-Design for manufacturing
-MIG soldering
-Sheet metal forming
-Automotive painting
-Car systems and integration
Administrative
-Financial & cost analysis
-Team operation under Project Management methodologies
Soft skills
-Leadership
-Self-learning
-Public relations a negotiation skills
-Teamwork and comunication
-Creativity