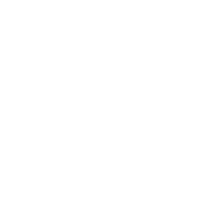
APEX PREDATORS ROBOTICS
Project
AUTONOMOUS BATTLE MINISUMO
Design challenge
Conceptualize, design and manufacture an autonomous mini sumo robot to fight and to compete with other autonomous robots in order to push the adversary out of the battle area bounded by a white circle. Employing 3D design tools such as Solidoworks, 3D printing, CNC machinning, PCB design, microcontrollers.
Role
Team Founder
Electronics & Software Leader
Chasis Design Leader
GENERAL RULES AND REQUIREMENTS
Robot restrictions
- There can be a maximum of 3 competitors per team;
- The robot must fit within the dimensions of 100×100 mm and weigh a maximum of 0.5 kg;
- The robot may increase its dimensions after the start, but must remain in one piece;
- The robot must wait 5 seconds after pressing the start button before it can start moving;
- The competition field is 77 cm in diameter and black in colour. The edge of the field 2.5 cm is white.
- The robot must drive autonomously. Remote control or any other form of control of the robot is prohibited.
- Sensors: Optical or ultrasonic (Professional level)
- Microcontrollers (No restriction)

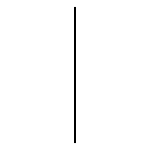
STARTING FROM SCRATCH
May 2022
This project started as an assignment for college, the main objective of the first prototype was to gain a sense of how microcontrollers worked, but we decided to take it to a higher level and built a much more advanced robot to compete in collegiate level competitions.
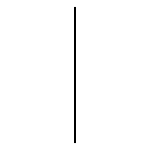
FIRST CONCEPT
June 2022
Our First concept of the robot was focused primarily on cost reduction using low-cost electronic components. The first problem that was found is that this components had bigger proportions compared to professional components, therefore a conventional setup for sensors and motors wasn´t possible, To address this issue, numerous iterations of the CAD design were carried out in SolidWorks in order to find the best possible configuration, using lateral thinking and design intent, without compromising functionality, reliability, structural reliability and cost reduction.
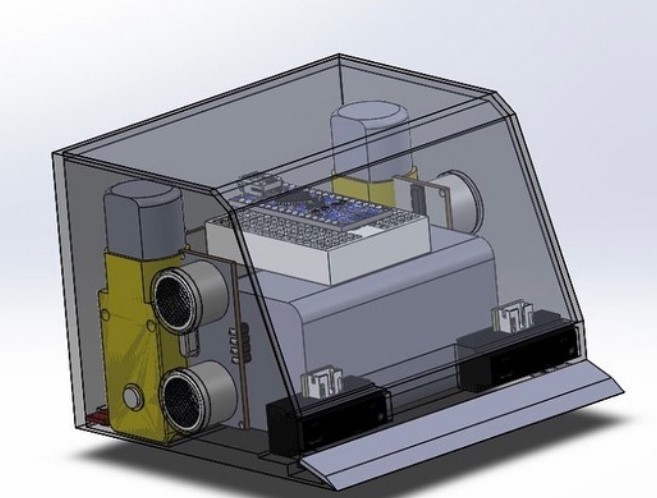
Materials
-ABS
-Stainless Steel front Razor Blade
Electronic Components
-2 9V Motoreductor 230 RPM
-1 1500mAh lithium battery pack
-1 Arduino Nano
-3 Ultrasonic sensors
-2 Optic sensors
In order to produce the first CAD model in Solidworks we executed reverse engineering on every single component that the robot had to use in order to produce an accurate 3D model that actually helped us predict any undesired interference between parts or any possible failure when having all systems combined. This approach allowed us to reduce assembly errors and avoid printing chasis multiple times.
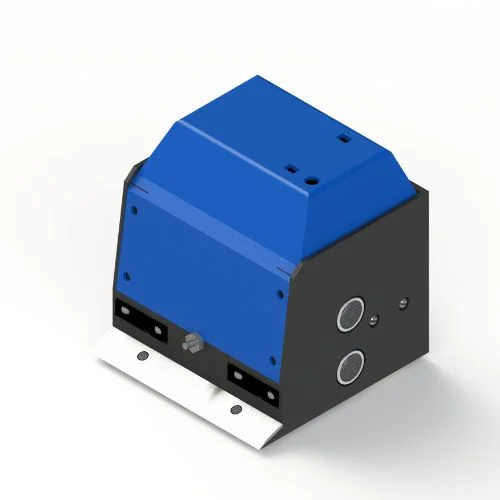
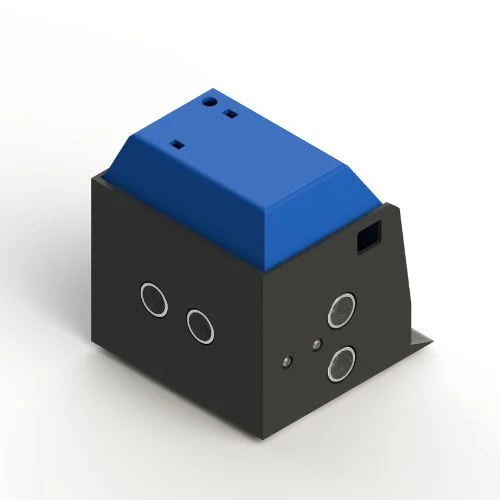
Achievements
Chasis design
–Low center of gravity design as batteries and most components were located as low as possible, improving robot’s stability and maneuverability.
-Chassis printed with high resistance ABS plastic which helped reduce wall thickness and increase space for components.
-CAD model of chasis considered every detail and dimension of each part ensuring no additional post processing after printing part, enabling an easier assembly process of sensors, motors and electronics to chasis.
Electronics
–Reduced costs of electronic components while ensuring proper functionality of the robot.
-We managed to organize connections of components to the microcontroller and mini protoboard in order to facilitate assembly.
Programming
-Despite using low-cost ultrasonic sensors we were able to program the behavior of a sumo built with more advanced sensors.
Issues identified
Chasis design
-As space was very well used there was very little space to work with in case any adjustment was needed or in case a failure ocurred, for example in motors and connections of electronics. Therefore, a chasis that could be easily dismaounted was needed.
Electronics
-As we had a big amount of electronic parts a lot of connections were needed and cables interfered with other components causing disconnections or failures and it was hard to detect where a failure was located.
Programming
-Improved attack and defense adjustments were needed for the strategy of the robot for more possible scenarios during battle.
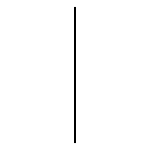
2ND ITERATION
For the second iteration we learned from all of our previous mistakes and perfected overall design and battle strategies, out robot was ready to compete and win international battles, we named Baba Yaga our robot in honor to John Wick film, since our robot had 8 sensors in total making it extremely good for detecting opponents and react in a fast manner.
This amount of sensors also made the code more complex but we managed to create the right amount of attack strategies to fully take advantage of the sensor arrangement, we also added light indicators to each sensors to know the actual state of these without the need to connect the serial plotter and monitor signals and facilitate the iterative process to calibrate sensor´s parameters.
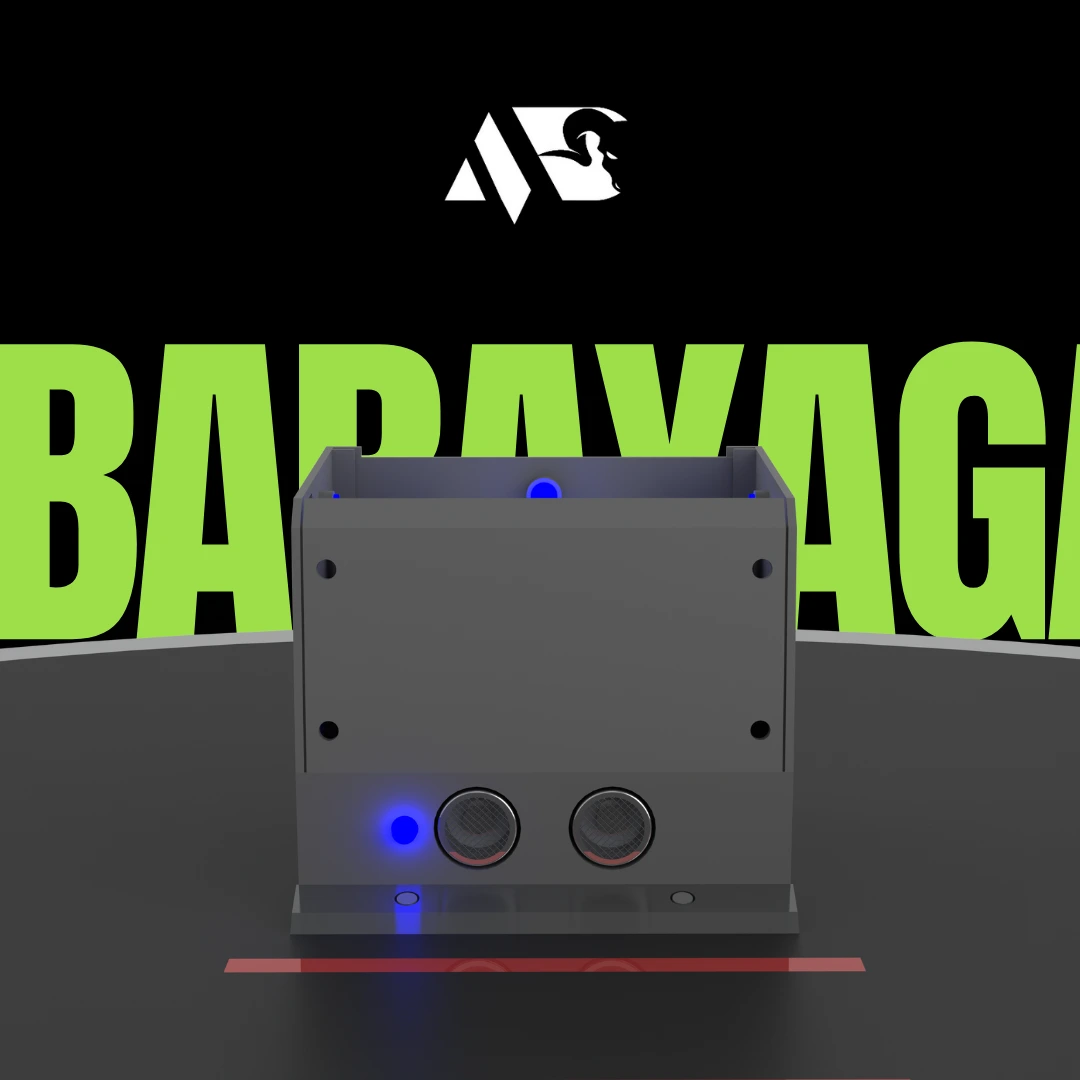
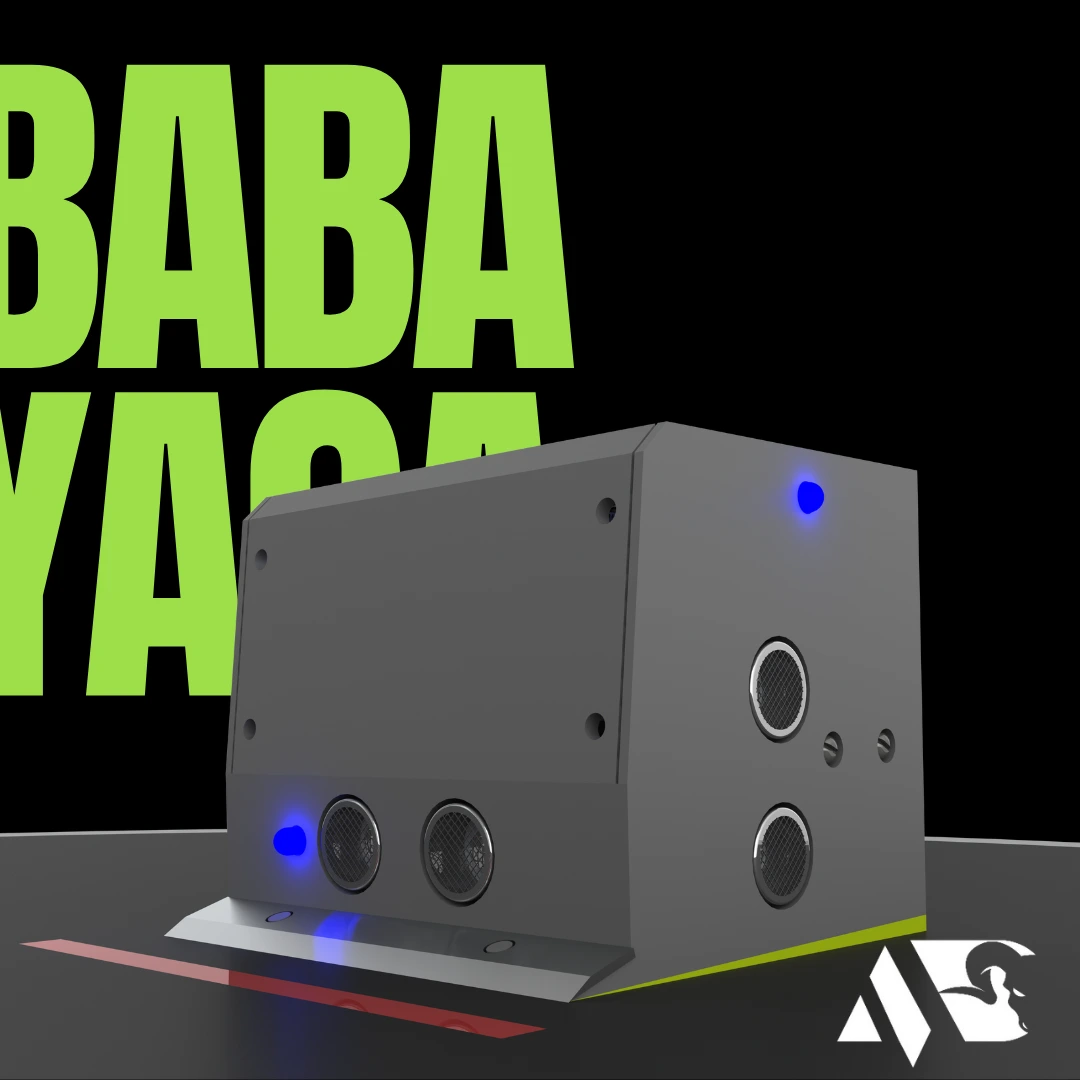
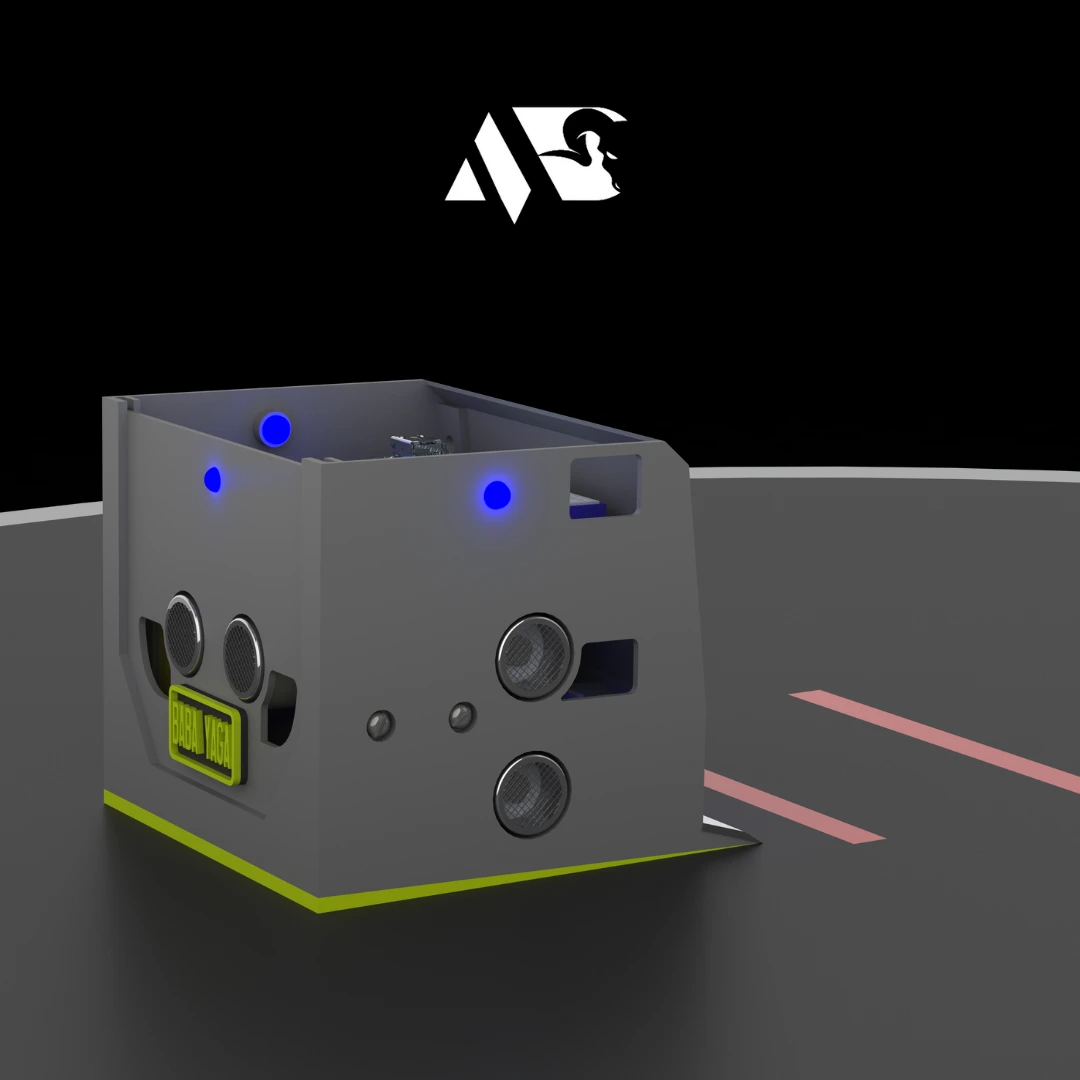
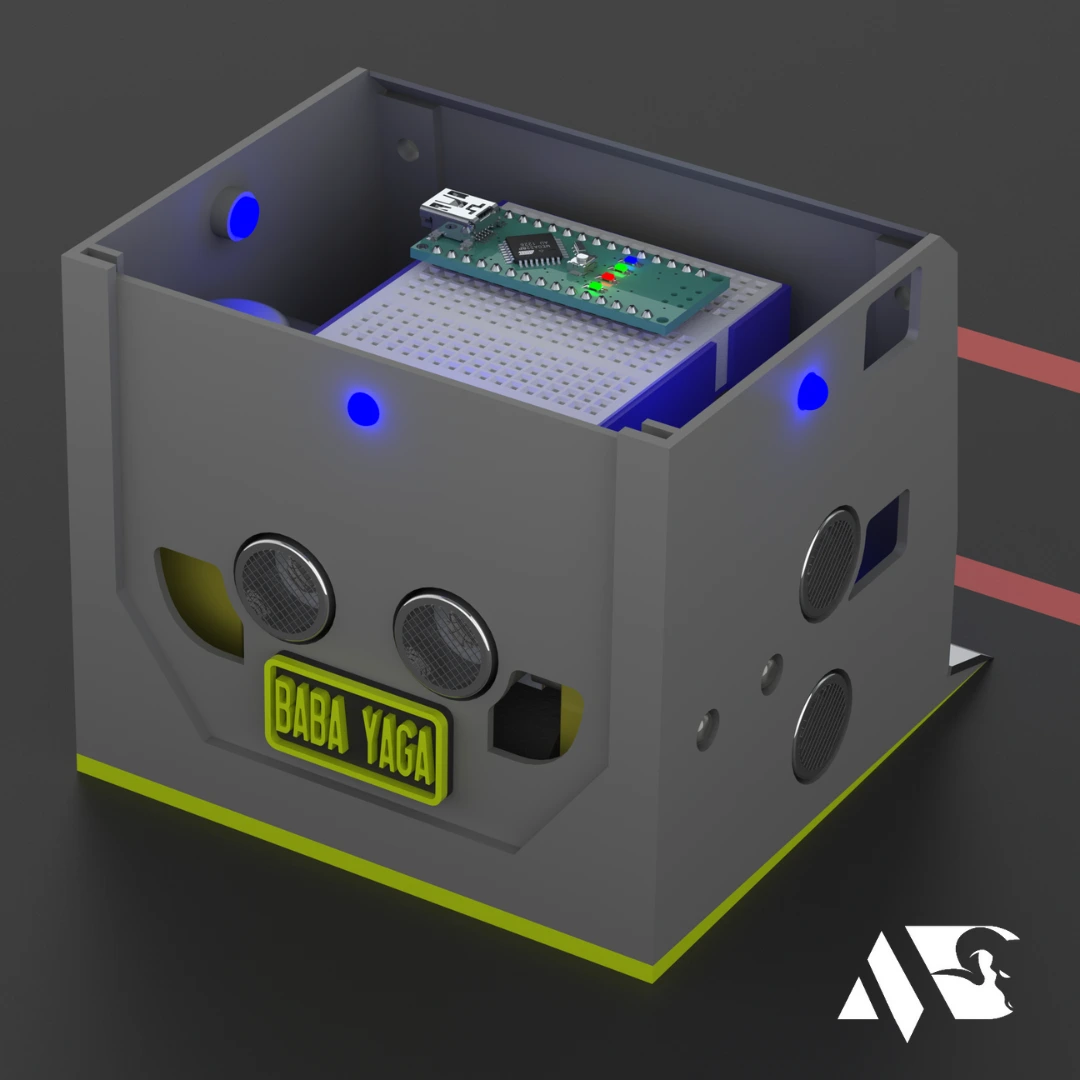
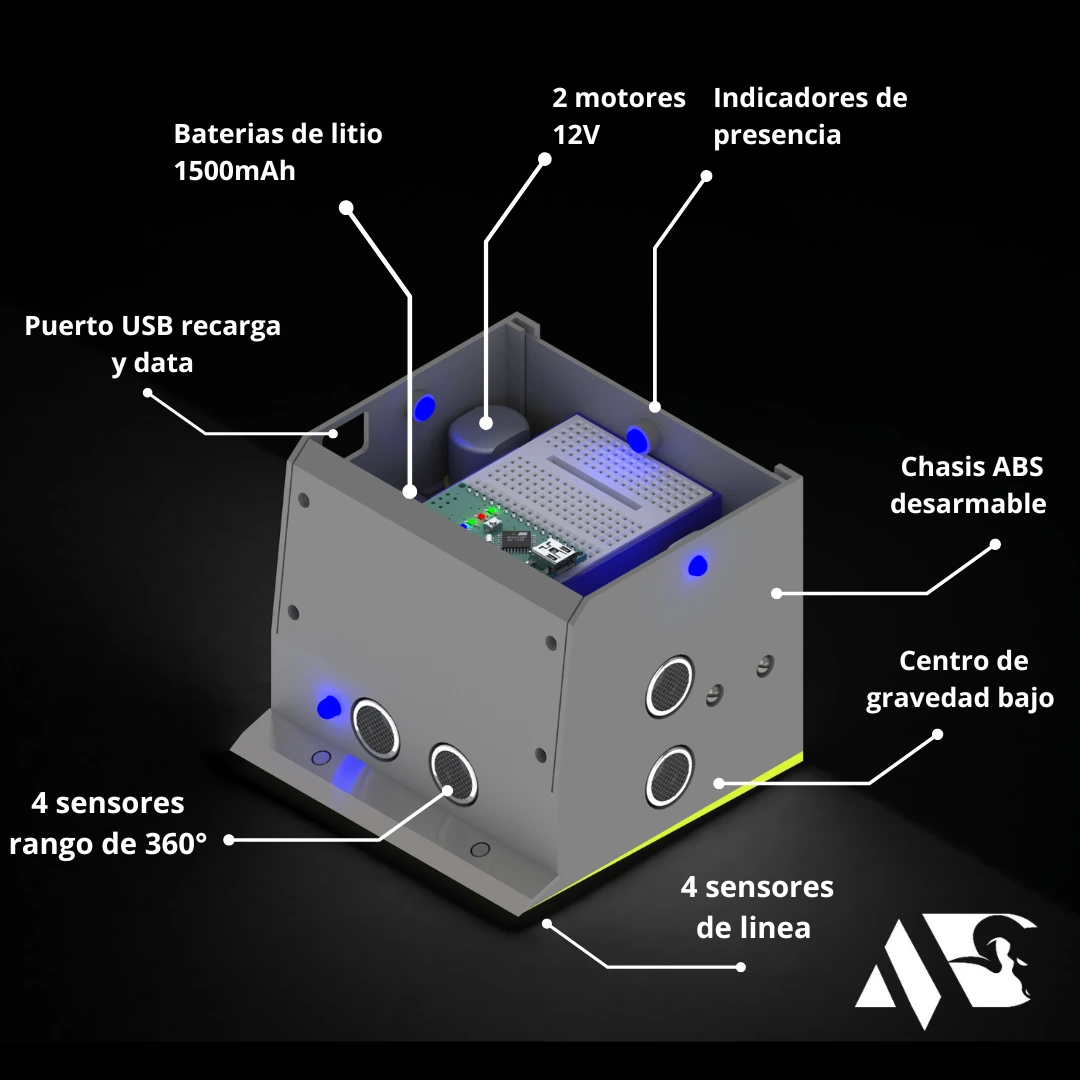
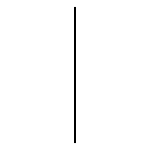
COMPETITION
In 2021, we registered for the international competition «Sumomania» in Morelos, Mexico. We fully complied with the tournament’s rules and restrictions and received financial support from Ph.D. Omar Abreo Rodriguez, a researcher and professor at UPQ, which allowed us to cover expenses related to competition.
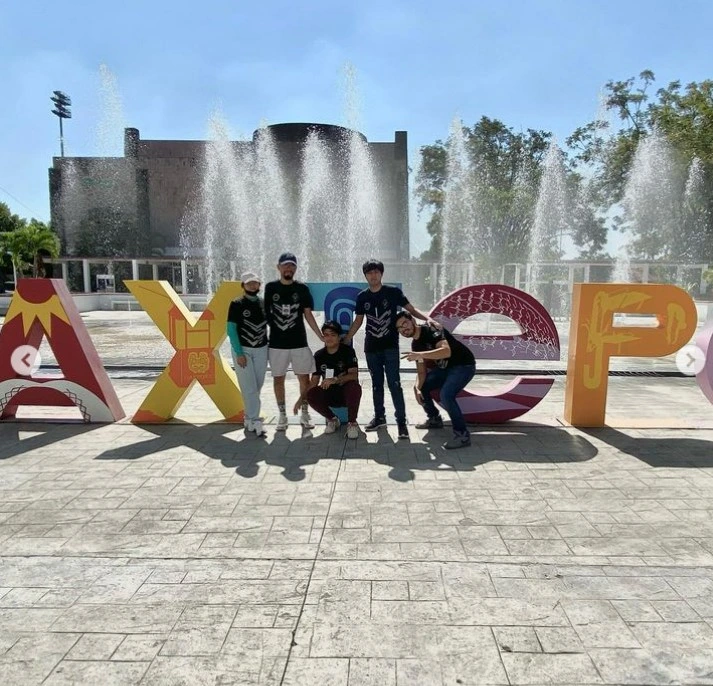
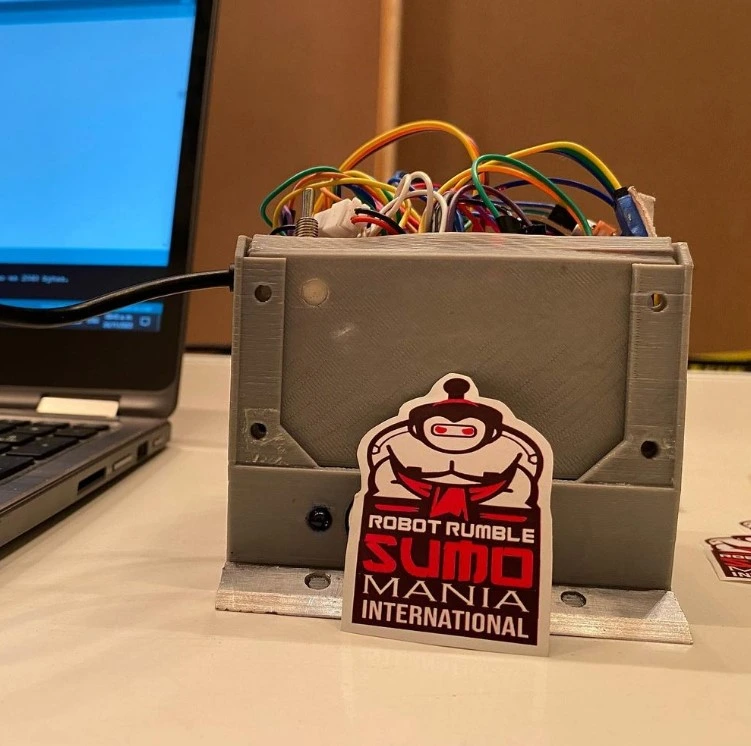
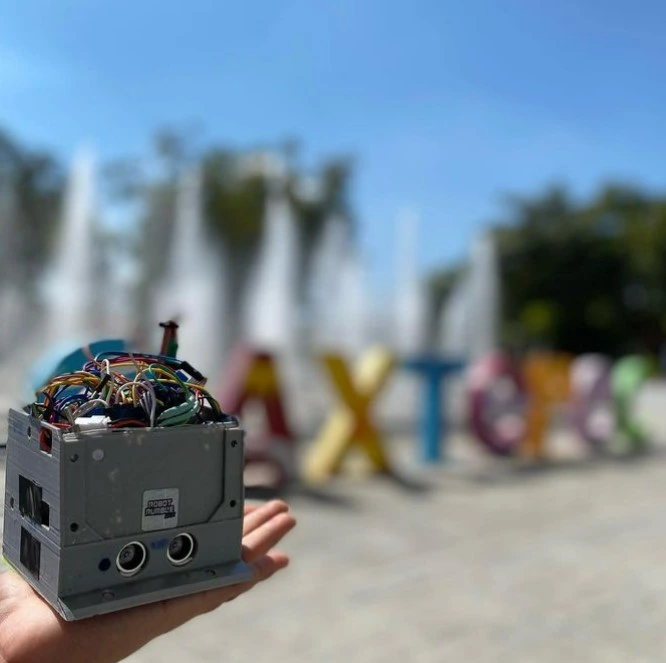
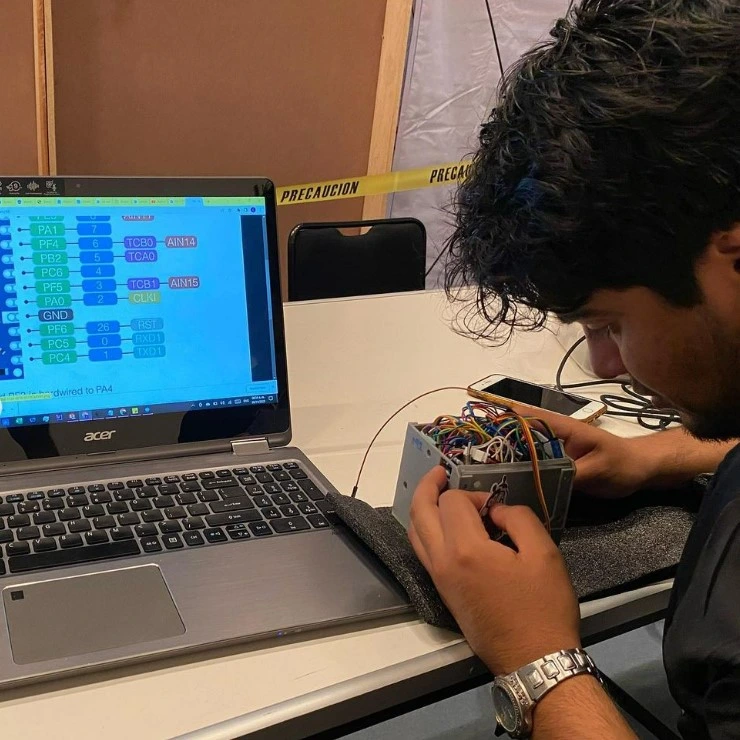
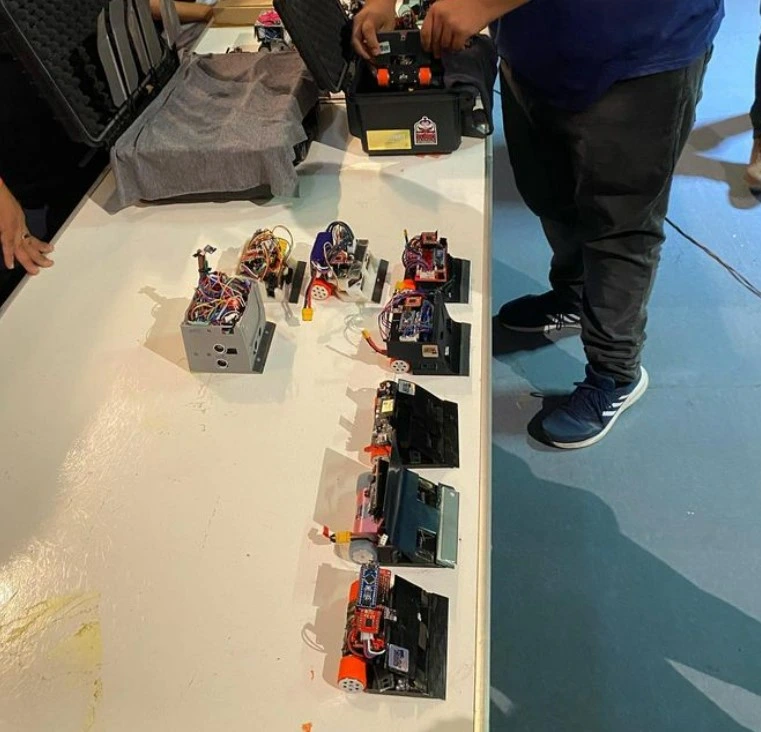
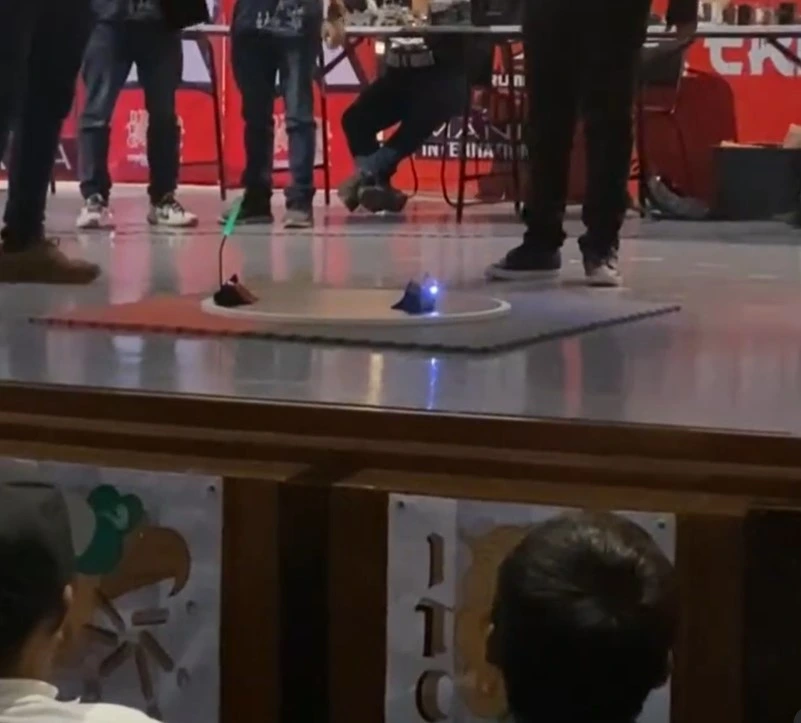
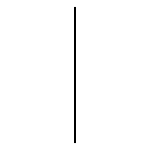
ACHIEVEMENTS
Despite it being our first competition, we achieved an outstanding 7th place out of 72 teams from around the world, including some of the best universities in Mexico. We returned home with the honor of representing our school and country.
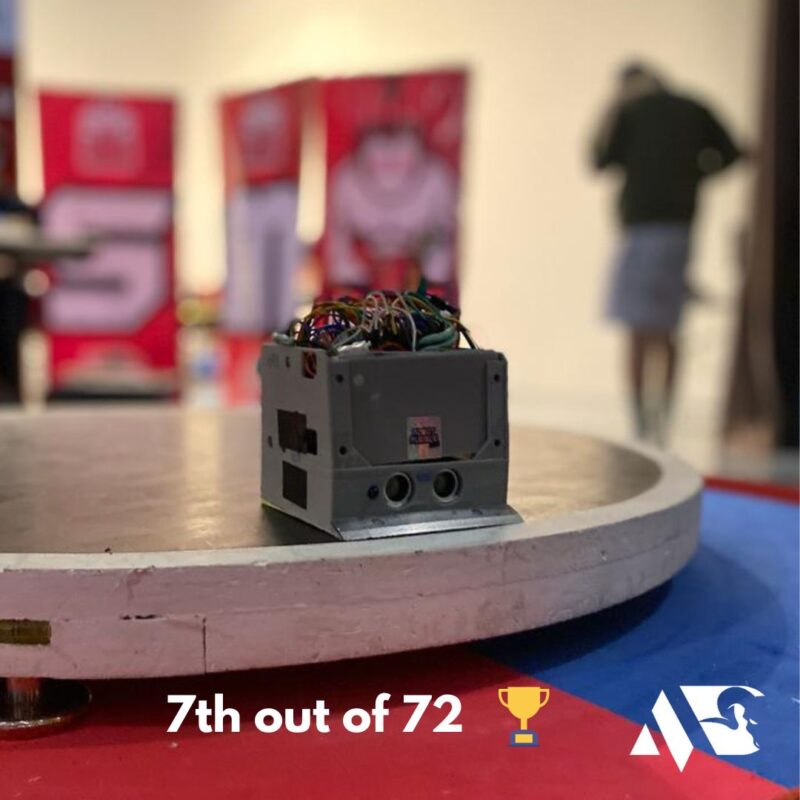
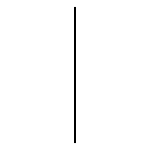
FUTURE DEVELOPMENTS
Our next robot has professional components and it has a lightweight machined aluminum chassis and the following improvements have been made:
Materials
-Aluminum 6061-T6
-Stainless Steel front Razor Blade
Electronic Components
-2 12V Fingertech professional motor-reductor 570 RPM
-1 1500mAh lithium battery pack
-1 Arduino Nano
-3 Optical proffesional sensors
-Printed PCB with custom design integrating all components
-100% Dismountable parts and connectors
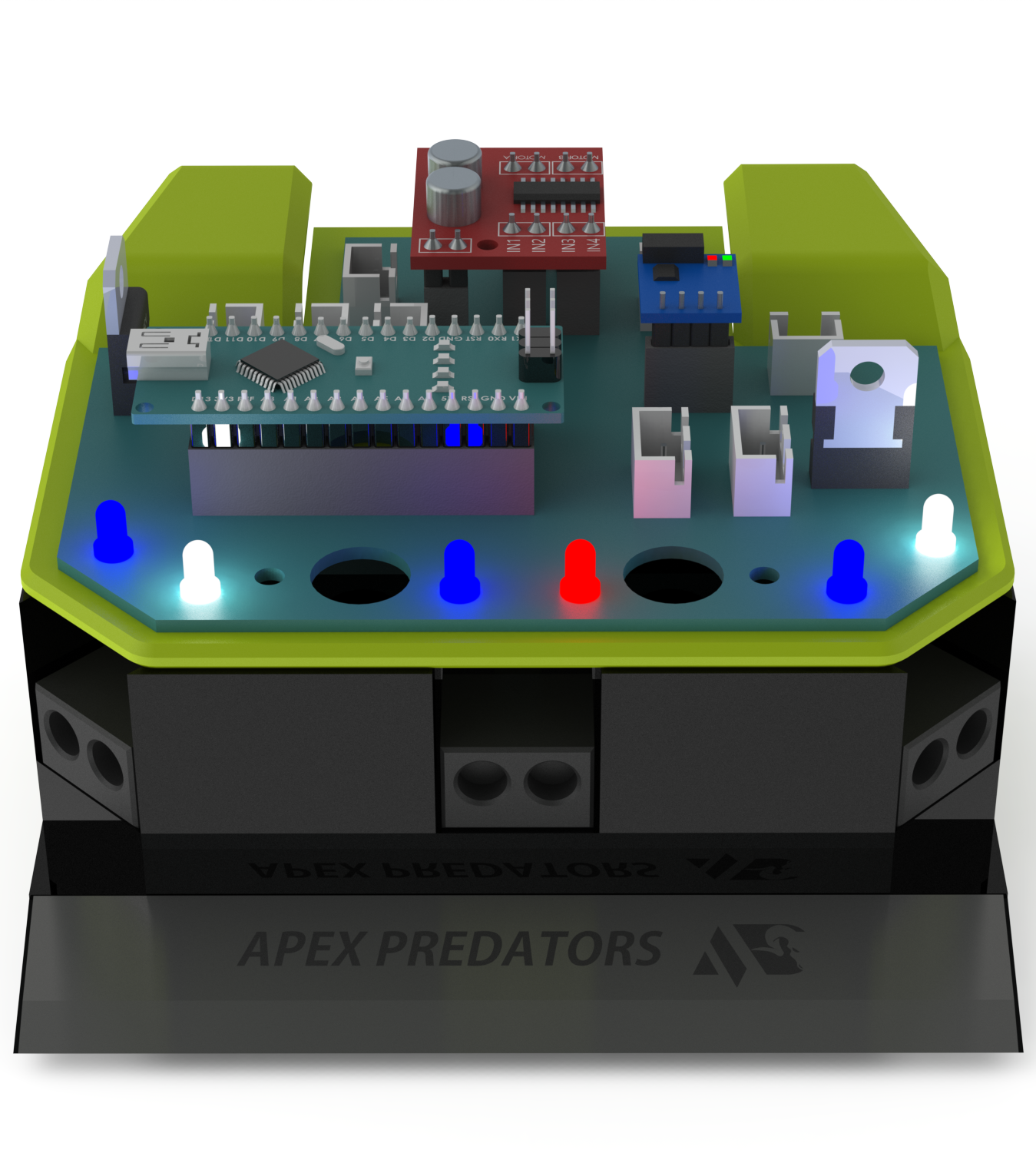
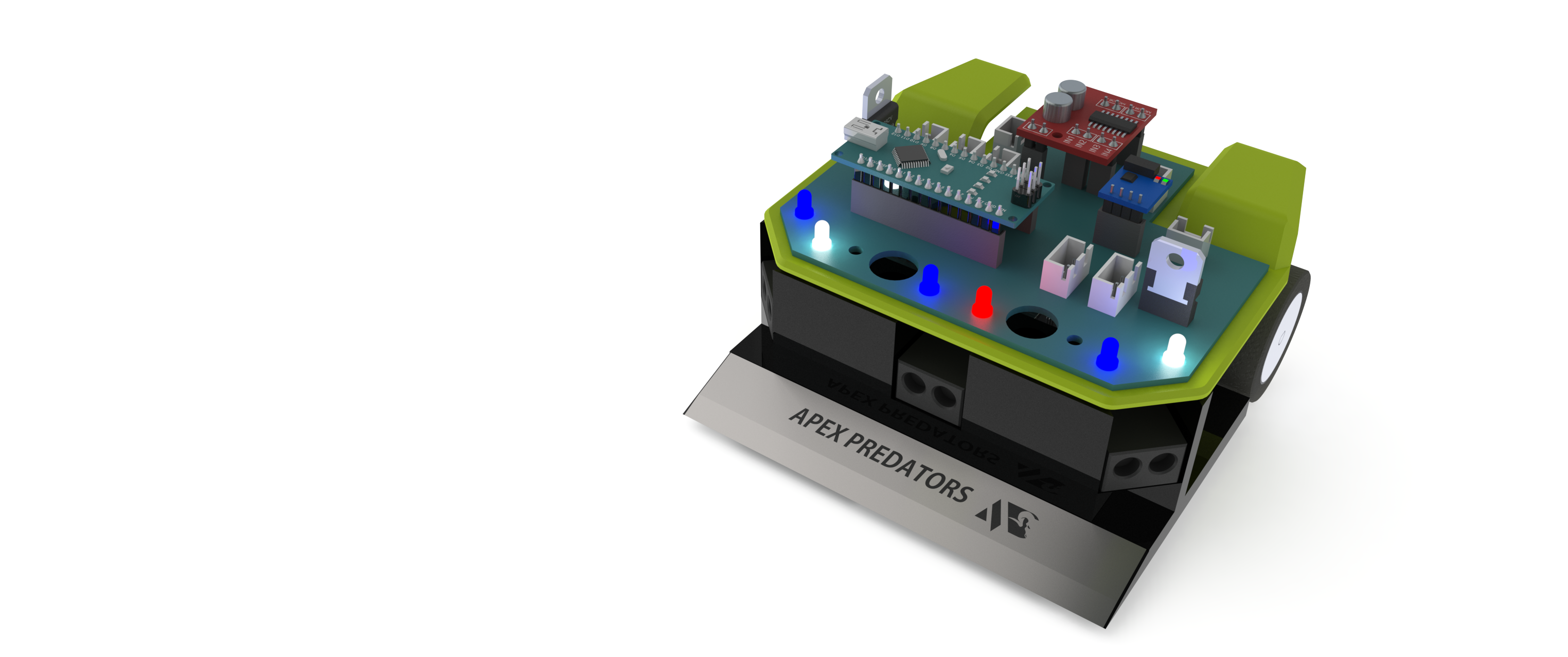
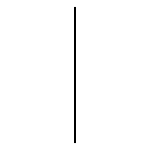
Our idea since the creation of this team is to leave a mark for future generations of engineers that want to compete and take projects to a further level to continue the team legacy and build more and better robots to compete, we are currently working with other students on building their own prototype to compete and obtain a better place next time.